Make Best Use Of Performance: Proactive Pipeline Welding Inspection Approaches
Make Best Use Of Performance: Proactive Pipeline Welding Inspection Approaches
Blog Article
Ensuring Security and Precision in Pipe Welding Inspection
In the realm of pipeline welding evaluation, ensuring safety and security and precision are critical goals that demand precise focus. The integrity of pipelines hinges on the quality of welds, making the inspection procedure a vital aspect of maintenance and building.
Significance of Pipeline Welding Inspection
Pipeline welding inspection is critical for making sure the stability and safety of the framework. With meticulous examination, prospective defects, such as splits, incomplete infiltration, or misalignments, can be spotted and rectified prior to they lead to disastrous failures.
Appropriate evaluation techniques, such as aesthetic testing, radiographic screening, ultrasonic testing, and magnetic fragment testing, are used to evaluate the quality of welds. These approaches help make certain that welds satisfy sector standards and regulatory needs. By determining and resolving defects early in the welding procedure, the risk of leaks, ruptures, and ecological contamination is substantially reduced.
Additionally, pipeline welding inspection plays an essential duty in preserving compliance with safety criteria and guidelines. Routine assessments not only boost the architectural integrity of pipes however also add to the total safety and security of employees and operations working in the area. Fundamentally, buying detailed pipe welding evaluation is an aggressive procedure to avoid pricey repair services, mitigate threats, and support the integrity of vital infrastructure.
Advanced Inspection Technologies
Advanced examination technologies play an essential function in making sure the honesty and safety of pipe systems. One of the most prominent developments in pipeline welding assessment is the usage of automated ultrasonic screening (AUT)
In addition, the execution of phased array ultrasonic testing (PAUT) has revolutionized the evaluation process by offering comprehensive imaging of welds in real-time. PAUT uses far better issue discovery capacities and enables fast data evaluation, enabling inspectors to make enlightened choices without delay - Pipeline Welding Inspection. In addition, electronic radiography (DR) has become increasingly popular in pipe welding examination as a result of its capability to create top quality images that enhance issue presence while lessening radiation exposure
Incorporating these sophisticated assessment innovations not only improves the top quality of weld assessments but also boosts general safety criteria in pipeline construction and upkeep.
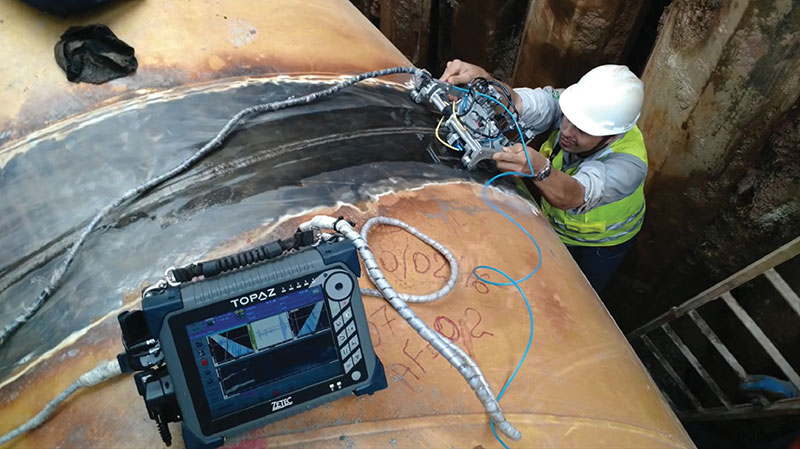
Duty of Trained Inspection Professionals
The integration of innovative examination innovations in pipe welding examination highlights the vital importance of trained examination professionals in ensuring the precision and dependability of assessments. Educated assessment professionals play a crucial function in supervising the execution of these innovations, interpreting the information obtained, and making educated choices based upon their know-how.

These professionals are outfitted with the required expertise and skills to carry out extensive inspections, determine possible problems or abnormalities in welds, and ensure compliance with market standards and policies. Their ability to assess data, identify patterns, and troubleshoot problems is crucial in keeping the stability and safety and security of the pipeline framework.
Additionally, trained evaluation experts work as a vital web link between technology and functional application. By leveraging their experience and training, they can give beneficial insights, referrals, and services to enhance the welding process and alleviate threats effectively.
Precaution in Welding Inspection
Efficient application of precaution in welding assessment is extremely important to making certain the protection of personnel and the integrity of the infrastructure. Welding inspection activities involve numerous threats such as direct exposure to fumes, electrical shock, and fire threats. To alleviate these risks, adherence to security procedures is crucial. Workers associated with welding inspection must wear ideal individual safety devices (PPE) such as helmets, handwear covers, safety and security glasses, and fire-resistant apparel to minimize the risk of injuries. Additionally, making sure appropriate ventilation in the welding area helps in decreasing direct exposure to unsafe fumes here are the findings and gases generated during the welding process.
Routine safety training sessions need to be carried out to enlighten evaluation specialists on the most recent safety procedures and protocols. It is crucial to have emergency action strategies in position to resolve any unpredicted cases immediately. Inspectors ought to be cautious in examining the welding tools routinely to determine any kind of potential security hazards. By prioritizing security actions in welding evaluation, companies can develop a protected working setting and promote the quality and dependability of pipe framework.
Ensuring Precision in Evaluation Practices
With a concentrate on careful interest to detail, achieving accuracy in examination techniques is important for making sure the high quality and stability of pipeline welding. Precision in company website inspection techniques entails sticking to rigorous criteria and standards to precisely analyze the welds for any defects or blemishes. Using sophisticated evaluation technologies such as ultrasonic testing, radiographic screening, and aesthetic evaluation methods is crucial in identifying also the smallest flaws that can jeopardize the security and functionality of the pipeline.
Ensuring precision in examination techniques likewise requires trained and certified examiners that have a deep understanding of welding processes, products, and market regulations. These assessors should have the capability to interpret assessment results precisely and make informed choices concerning the approval or being rejected of welds based upon predefined requirements.
Normal calibration and maintenance of evaluation equipment are extremely important to guaranteeing the integrity and accuracy of assessment outcomes. By supporting high criteria of precision in examination practices, stakeholders can have self-confidence in the structural stability and efficiency of pipe welds, eventually adding to the total security and performance of the pipeline system.
Final Thought
In verdict, the significance of pipe welding evaluation can not be overemphasized. Advanced inspection innovations and experienced inspection experts play a crucial role in guaranteeing safety and security and accuracy in welding practices. By following stringent security click for info procedures and keeping precision in examination procedures, the integrity of pipelines can be supported, securing versus prospective dangers and making sure the proceeded performance of the system.
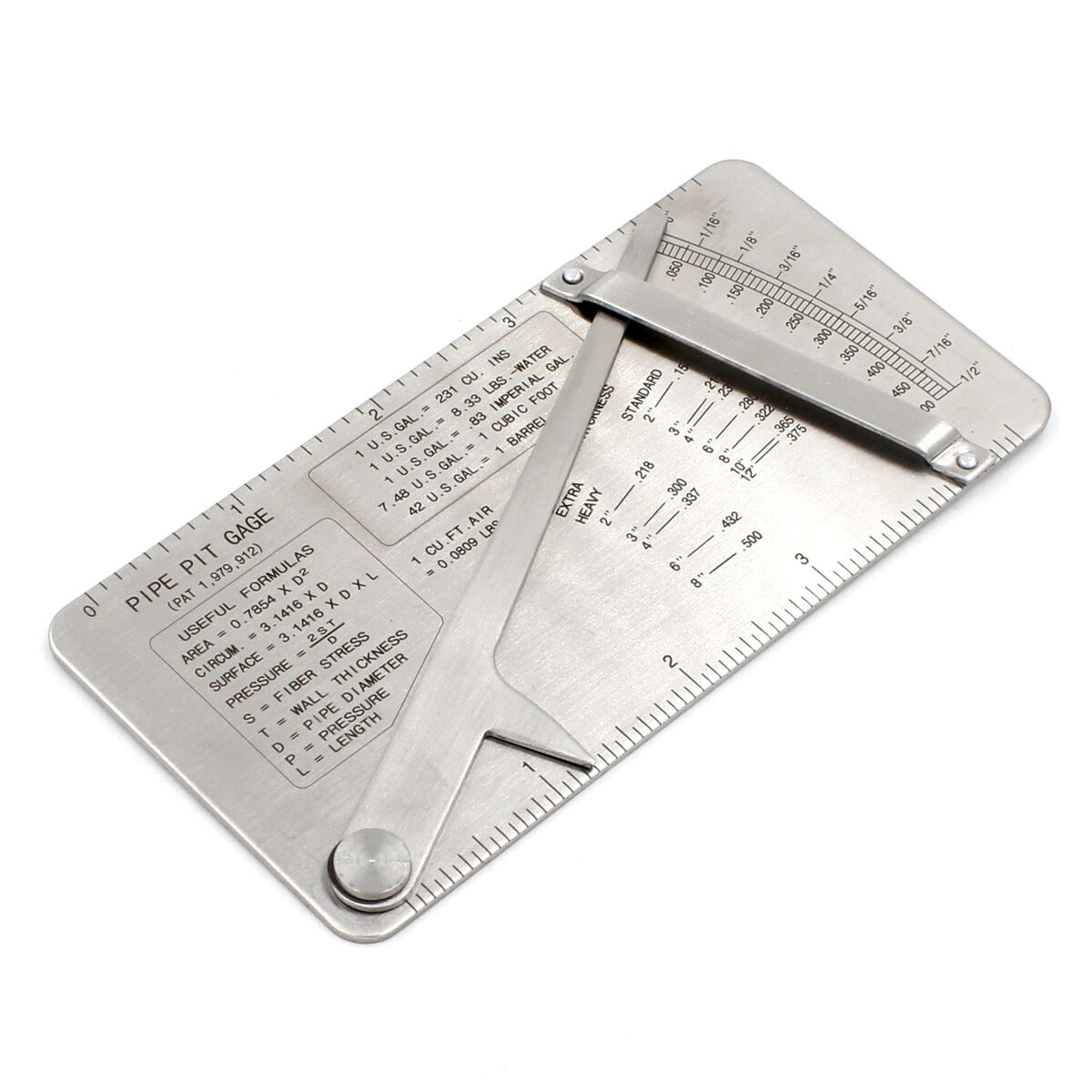
Utilizing innovative evaluation technologies such as ultrasonic testing, radiographic screening, and aesthetic examination approaches is crucial in identifying also the tiniest problems that might compromise the safety and capability of the pipe.
Advanced examination modern technologies and skilled evaluation professionals play a crucial duty in making certain safety and precision in welding techniques.
Report this page